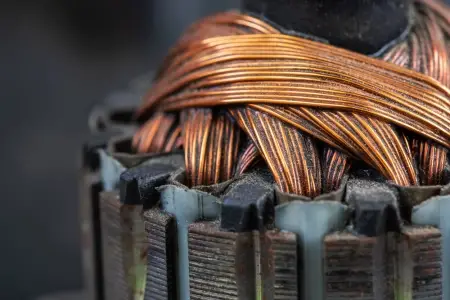
A commutator is an essential component in direct current (DC) electric motors and some electric generators. Its main function is to act as a mechanical rectifier and rotary switch, allowing periodic reversal of the direction of current in the rotor windings. This process is known as commutation.
The commutator is made up of segments of hard electrolytic copper, insulated from each other by a dielectric material such as mica. These segments are mounted on the rotor shaft and connected to the armature windings. To ensure current transmission, the commutator interacts with carbon brushes, which are kept in constant contact with its surface.
How does the commutator of an electric motor work?
The commutator consists of a set of contact bars fixed to the rotating shaft of the motor and connected to the armature windings. Its operation is based on the following principles:
- When the rotor rotates, the carbon brushes slide over the commutator segments, allowing the electric current to be conducive to the armature windings.
- As the rotor completes half a revolution, the commutator's connection to the brushes changes, reversing the direction of current in the winding.
- In a DC motor, this current reversal generates a magnetic field in the armature that interacts with the fixed field of the stator, producing a constant torque that keeps the rotor turning in a single direction.
- In a generator, the mechanical movement of the shaft generates an alternating current in the armature windings, which is then rectified by the commutator to obtain direct current in the external circuit.
- The number of segments in the commutator influences the smoothness of the switching: the more segments there are, the smoother the current transition, reducing sparking and brush wear.
- The design of the commutator and brushes must ensure efficient contact to minimize contact resistance and excessive heat generation, factors that can affect motor efficiency.
- A well-designed commutator enables stable motor performance by reducing electrical noise and optimizing current transfer between moving and stationary parts of the system.
- In the automotive field, specialized variants such as the automotive switch and the car switch are used , which enable efficient switching in electric vehicle starting and drive systems. A specific case is the starter switch , used in automobile starter motors to ensure reliable activation of the internal combustion engine.
Types of switches
There are various types of switches, designed to suit different applications and operational requirements. The most relevant ones are described below:
Drum switch
Common in higher power motors, this type of commutator is composed of copper segments arranged in a cylindrical shape around the rotor axis. Its robust design allows it to handle high currents and is common in industrial motors and electric traction systems.
Disk switch
Although less common, this type is characterized by having flat segments arranged on a rotating disk. It is used in specific applications where a more compact and lightweight design is required, such as in certain electronic devices and small motors.
Multi-segment switch
Designed for applications requiring smoother, more efficient switching, this type of commutator incorporates a greater number of segments, reducing sparking and improving motor stability. It is used in precision motors, high-speed power tools and advanced control systems.
Switch wear and maintenance
Due to continuous friction with the carbon brushes, the commutator is subject to wear over time. Some common problems include:
- Uneven wear : Can cause excessive sparking and poor switching.
- Dirt and carbon residue : Build-up on the surface of the switch can affect electrical contact.
- Brush misalignment : Can cause accelerated wear and loss of efficiency.
Commutator maintenance includes regular cleaning, inspection of brush wear, and in some cases, grinding the commutator surface to restore proper operation.
What is the purpose of the commutator in an electric motor?
The commutator performs several fundamental functions in the operation of direct current electric motors and generators:
- Electrical connection : Establishes a connection between the stationary brushes and the rotor windings on the rotating shaft.
- Change of current direction : When rotating, it reverses the polarity of the current in the rotor windings at the precise moment, ensuring a constant torque in the same direction.
- Angular position sensor : Its design allows the position of the rotor to be detected in relation to the magnetic field.
- Current conversion : In direct current generators, it transforms the alternating current induced in the windings into a direct output current.
In an alternator, the alternating current generated by the rotor's motion through the fixed magnetic field is converted into direct current voltage by the commutator. In an electric motor, the periodic reversal of current in the rotor windings allows the armature to continue rotating continuously.