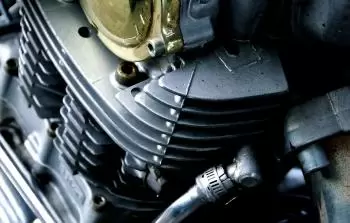
Diesel engines have several advantages over other internal combustion engines:
Advantages related to diesel engine fuel
The fuel of a diesel engine has a higher energy density and a smaller volume of fuel is required to perform a specific amount of work.
Diesel engines inject fuel directly into the combustion chamber, have no air intake restrictions other than air filters and intake pipes and have no vacuum in the intake manifold to add parasitic load and pump losses to push the pistons down against the vacuum of the intake system. Cylinder filling is aided by atmospheric air and volumetric efficiency is increased for the same reason.
The heavier fuels of the diesel engine, such as diesel fuel, have higher cetane rates and lower octane ratings, resulting in a greater tendency to ignite spontaneously and burn completely in the cylinders when injected. Increased compression ratios create higher temperatures in the combustion chamber to ignite the injected fuel.
Higher compression ratios increase pumping losses since more work is required to compress the intake air at a lower volume, but increases in pumping loss are compensated for by higher power and efficiency.
The increase in compression ratios in spark ignition engines requires higher octane fuels compared to the diesel engine. Otto motors are more difficult to ignite and completely burn and / or synchronize with advanced spark to avoid pre-ignition, knocking and resulting loss of performance and damage to the engine.
The compression ignition engine fuel is distilled directly from the oil. The distillation produces some gasoline, but the yield would be inadequate without a catalytic reform, which is a more expensive process.
Although diesel fuel will be burned outdoors with a wick, it will not release a large amount of flammable vapor that could cause an explosion. The low vapor pressure of diesel is especially advantageous in marine applications, where the accumulation of explosive mixtures of fuel and air is a particular hazard. For the same reason, diesel engines are immune to steam blockage.
For any given partial load, the fuel efficiency (mass burned for energy produced) of a diesel engine remains almost constant, unlike gasoline and turbine engines that use proportionally more fuel with partial power outputs.
Better efficiency in the diesel engine
Due to the previous differences in diesel fuels versus gasoline and other spark ignition fuels, diesel engines have a higher thermodynamic efficiency, with a heat efficiency of 45% compared to about 30% for ignition engines by spark. Gasoline engines are typically 30% efficient, while diesel engines can convert more than 45% of the fuel's energy into mechanical energy (see the Carnot cycle for a more detailed explanation).
Lack of electrical system
Diesel engines do not have a high-voltage electric ignition system or spark plug, which results in high reliability and easy adaptation to humid environments. The absence of coils, spark plug wires, etc., also eliminates a source of radio frequency emissions that can interfere with navigation and communication equipment, which is especially important in marine and aviation applications, and to avoid interference with radio telescopes.
The lack of an electric ignition system in the compression ignition engine also reduces the parasitic load on the engine, since the engine does not have to produce the electricity needed to ignite the fuel. A significant amount of electricity is required by a spark ignition system and, as engine speeds and loads increase, the ignition system consumes proportionally more electricity, while becoming less efficient.
A higher cylinder pressure requires a "hotter" spark with more current to overcome the pressure and jump the gap between the electrode and the electrode in the spark plug. The increase in engine speeds and loads also requires that the spark occurs more quickly, resulting in additional loads and demands on the electrical system and greater motor power to meet them.
As the speeds and loads of the diesel engine increase, the higher cylinder temperatures after the compression of the intake charge result in an increase in injection and the efficiency of the ignition due to the increased atomization of the fuel . Regardless of the fuel system design, a mechanical fuel injection system and rapid increase in pressure and fuel flow will result in the injection nozzle opening pressure being reached more quickly and earlier in the fuel cycle. 4 times and built-in timing advance.
Additional power is required to operate the injection system as the engine speeds and loads increase, but the increase is more compensated than in spark ignition engines. Modern diesel engines with electronic injection systems use a large amount of electricity for injection.
Diesel engine longevity
The longevity of a diesel engine is generally about twice that of a gasoline engine due to the greater strength of the parts used.
Advantages in the lubrication of the motor
Diesel fuel has better lubrication properties than gasoline too. In fact, in unit injectors, the fuel is used for three different purposes: injector lubrication, injector cooling and injection for combustion.
Although spark ignition engines and their fuel systems do not require as much lubricity, the higher lubricity of diesel fuel helps provide lubrication to the top of the cylinders and piston rings where it is most needed to withstand the high heat, loads and compression and combustion friction. Because diesel fuels are actually very light oils, excess fuel in the cylinders and oil contamination of the crankcase is more easily tolerated by diesel engines.
Biodiesel
Biodiesel is an easily synthesized fuel, not derived from petroleum (through transesterification) that can work directly in many diesel engines, while gasoline engines need adaptation to work with synthetic fuels or use them as an additive to gasoline (for example, ethanol added to gasohol).