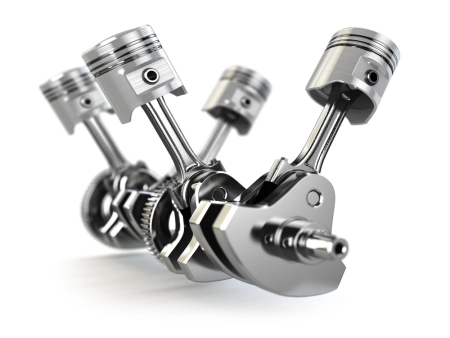
A piston is an element made up of two parts: a plunger that moves in a rectilinear reciprocating motion and a sleeve or guide in which it moves. This guide is sometimes also called a cylinder. In principle, the piston has a cylindrical shape and is usually made of metal, although it could be made of any material.
The guide is actually a cavity that can be integrated into a different part. It is part of the piston-connecting rod-crank system that is used to transform rectilinear movements into rotary ones and vice versa.
As a definition of piston, we can say that a piston is a part of a pump or engine cylinder that moves driven by a fluid or by the explosion of fuel: The piston of an engine connected to the connecting rod.
In machines where the piston has a cylindrical or oval shape, the piston is often coupled to the crankshaft with the connecting rod. There are often piston rings around the piston. The function of the piston rings is to ensure that there is a good seal between the cylinder wall and the piston.
Function of the piston in a thermal engine
The function of the piston is to absorb the heat energy caused by the explosion of the fuel and convert it into linear kinetic energy moving downwards. The speed and power with which the piston moves depends on the resistance of the engine and the intensity of the explosion. According to the second law of thermodynamics, the converted energy will always be less than the thermal energy of the explosion.
In a car internal combustion engine, the piston is traditionally called the cylinder. In a car, the cylinder is a cylindrical piece of steel. The movement of the piston is due to the fuel being periodically drawn into the cylinder head. Although the most common fuel is gasoline in Otto engines or diesel in diesel engines, there are also engines that run on gas and other elements.
As a result of motion, a liquid or gas is displaced, or compressed, by pumps and compressors. In engines, work is done on the piston by gases, which can then be transferred to other components, such as the crankshaft.
Operation of a reciprocating engine piston
In the case of Otto engines, a spark from a spark plug is needed to operate. In this case, they are also called spark ignition engines. The combination of the three elements causes a controlled explosion that pushes the piston plunger away, thus generating a movement. This movement is transmitted to the crankshaft. The pistons are placed alternately on the crankshaft, so that those that are pushed out push the others in, and then those that have been left further back will be the ones that push the previous ones back in.
In the case of diesel engines, the operation is the same. The main difference between them is that the fuel explosion is not caused by a spark but by increasing the pressure.
The crankshaft is the part of an engine that converts the linear alternating motion of the piston into circular motion.
This occurs in engines that are called reciprocating or, more formally, reciprocating motion. At the end of each piston, in addition to the air and fuel inlets, the mixed air outlet produced by combustion, and the spark plug, there are grooves where the compression and lubrication rings are assembled.
The lubricant is used to reduce the friction force of the piston inside the cylinder liner. At the opposite end, the piston has a hole where the pin that connects the piston to the connecting rod is housed.
A piston valve is a mechanism used to control the movement of a fluid through a pipe by means of the linear motion of a piston within a cylinder. It is used, among others, in most current brass instruments.
Features of a piston
The true cold shape of the piston is not cylindrical, as the mass distribution and operating temperatures are uneven, and this leads to uneven expansion. Its shape is more or less truncated-conical in section (in reality, the maximum diameter is usually about 10 mm from the lower edge of the mantle) and oval in plan, where the lower axis passes through the pin and its flow-ways.
The precise shape for each engine and application is defined with computer simulations and operational tests, so that at operating temperature it assumes the correct shape to ensure the lowest oscillations in the barrel, correct lubrication, lowest frictions and the most effective sealing against combustion gases.
In addition to the classic shapes, there are also pistons, generally for rotary engines, where the shape is completely different, as in the case of the Wankel engine, where the piston or rotor has a trochoidal shape, but there is also the case of a classic engine (with alternating pistons) where these, instead of the usual round section, have an oval profile.