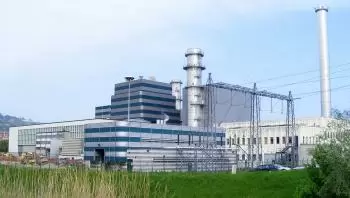
Cogeneration is a process that allows the simultaneous production of electrical and thermal energy from the same primary energy source. The heat generated can be used for heating, cooling or in industrial processes, which significantly improves energy efficiency compared to conventional generation.
Characteristics of cogeneration plants
Cogeneration plants have a number of features that make them efficient and attractive for the simultaneous production of electricity and heat. Some of the main characteristics of these facilities are:
High energy efficiency
The main advantage of cogeneration plants is their ability to make the most of the energy in fuels by simultaneously producing electricity and useful heat. This improves the overall efficiency of the system, reaching values above 80%, compared to 40-50% for traditional power generation plants.
Use of waste heat
One of the key features of cogeneration plants is the recovery and use of waste heat, which is used to heat water or air, or for industrial processes that require heat. This reduces the need to use additional resources to generate heat.
Versatility in fuel
Cogeneration plants can run on different types of fuels, including natural gas, coal, biomass, biogas, and industrial waste. This gives them the flexibility to adapt to changing economic and environmental conditions.
Reducing emissions
By making better use of fuel, cogeneration plants generate fewer emissions of polluting gases per unit of energy produced, which contributes to a smaller carbon footprint. However, the intensity of emissions depends on the type of fuel used.
Distributed generation
Cogeneration plants can be installed in a decentralised manner, allowing energy production closer to the place of consumption (e.g. in industrial plants or large buildings). This reduces the losses associated with transporting electricity over long distances.
Operational flexibility
Cogeneration plants can easily adjust to different demands for electricity and heat. This adaptability makes them especially useful in installations that require both types of energy simultaneously.
Cost reduction
Cogeneration allows savings in energy costs, as fuel use is optimised. Companies that require both electricity and heat (such as in industrial processes or large heating installations) can significantly reduce their energy bills.
Reduced environmental impact
Since these plants are more efficient, resource consumption and emissions of polluting gases are lower than in conventional plants. This makes them more sustainable compared to other forms of energy generation.
Ability to integrate with other renewable sources
Cogeneration plants can also be integrated with renewable energy sources, such as biomass, allowing them to further increase the sustainability of the operation.
Performance on a small or large scale
These plants can be designed for operations of different scales, from small installations for industrial or residential use to large plants that supply energy to electrical grids or district heating systems.
Components of a cogeneration plant
The main components of a cogeneration plant include:
- Engine or turbine: This can be gas, steam or biomass. This component converts the energy from combustion or steam into mechanical energy, which is then converted into electricity by an electric generator.
- Heat generator (boiler): Uses waste heat from the electricity generation process or direct combustion of fuels to produce steam or hot water.
- Heat Recovery Steam Generator (HRSG): In combined cycle plants, waste heat from the turbine exhaust gases is used to heat water and generate steam that can be used for heat production or to drive an additional steam turbine.
- Heat distribution system: A system of pipes and pumps to transport the heat produced to the areas of use, such as industrial, residential, or industrial process heating.
- Electric generator: A generator that converts mechanical energy from turbines (both gas and steam) into electricity.
- Emission control: Filters and gas treatment systems to control the release of pollutants into the atmosphere, such as nitrogen oxides (NOx), sulfur dioxide (SO2) and particulate matter.
- Cooling systems: In some plants, cooling towers or heat exchangers are used to reduce the temperature of the steam used and ensure process efficiency.
Examples of cogeneration
Here are some relevant examples of cogeneration in different sectors:
- Paper Industry : The Spanish company Saica uses cogeneration to supply its recycled paper factories, achieving greater energy efficiency and reducing emissions.
- Hospitals : Many hospitals in Europe and the US, such as Hospital Clínic in Barcelona, have implemented cogeneration systems to ensure a stable energy supply and reduce costs.
- Automotive Sector : In 2009, Volkswagen launched a project to install 100,000 mini cogeneration plants in homes and small businesses in Germany, with a total capacity of 2 GW.
- Wastewater Treatment Plants : In several cities, such as Madrid and Chicago, cogeneration systems are used that convert the biogas generated into electricity and heat for their own operation.
- Buildings and Hotels : Some hotels, such as the Ritz-Carlton in San Francisco, have implemented cogeneration to optimize their energy consumption and reduce operating costs.
Applications of cogeneration
Thermal energy generated in cogeneration systems can be used for:
-
Industrial applications.
-
Environmental heating and cooling systems.
-
District heating networks.
Cogeneration plants can operate with fossil fuels (natural gas, fuel oil) or with renewable fuels (biomass, biogas, synthesis gas), allowing considerable energy savings compared to the separate generation of electricity and heat.
Energy efficiency in cogeneration
The efficiency of a cogeneration system is measured by considering both the electrical and thermal energy generated. For example, a plant that consumes 100 MWh of methane gas to produce 40 MWh of electricity and 40 MWh of heat has an overall efficiency of 80%, much higher than that of a conventional plant.
Other key indicators for assessing efficiency include:
-
Fuel efficiency: Ratio of net electricity produced to fuel consumption.
-
Energy Savings Index (ESI): Measures energy savings compared to separate generation.
-
Utilization coefficient: Sum of the electrical and thermal efficiencies.
-
Economic savings index: Evaluates the profitability of cogeneration based on avoided energy costs.
Types of cogeneration plants
1. Combined cycle cogeneration plants (Gas-Steam)
Combined cycle cogeneration plants are one of the most efficient options for the simultaneous production of electricity and heat. This system combines a gas turbine and a steam turbine.
The process begins with the combustion of natural gas or some other fuel in the gas turbine, generating electricity. The exhaust gases from this turbine, which still contain a significant amount of thermal energy, are channeled to a steam generator, where it is used to heat water and produce steam. This steam is then directed to a steam turbine which generates additional electricity, making the most of the energy contained in the fuel.
One of the main advantages of this type of cogeneration is its high efficiency, which can exceed 80%, since both electricity and waste heat are used. This configuration is particularly beneficial for large industries or plants that require both electricity and heat continuously, such as in industrial processes, district heating or power plants.
The flexibility in the type of fuel that can be used also makes these plants an attractive option for a variety of applications, including those seeking to reduce their carbon footprint and improve energy sustainability.
2. Natural gas cogeneration plants (Gas Turbine)
Cogeneration plants using gas turbines are popular for their ability to efficiently generate electricity and heat. These plants operate by burning natural gas in a turbine, which generates electricity through the movement of the turbine blades.
The waste heat from the combustion process is used to heat water or produce steam, which can then be used for industrial processes, heating, or in other systems that require heat. This configuration is common in plants operating near residential or industrial areas, where the heat can be used directly.
Natural gas is a relatively clean fuel compared to other fossil fuels, making these plants more sustainable and with lower CO₂ emissions. Although the efficiency of these plants can vary, the combination of electricity and heat produced together allows for reduced resource use and improved plant performance.
These plants are especially useful in areas where the demand for heating and electricity is constant, such as hospitals, residential complexes or large commercial facilities.
3. Biomass cogeneration plants
Biomass cogeneration plants use renewable resources, such as agricultural, forestry or food waste, to generate electricity and heat.
The process involves the combustion of biomass, which releases thermal energy, which is used to heat water or produce steam. This steam, in turn, drives a steam turbine to generate electricity. Cogeneration in this type of plant is especially beneficial for rural regions or where organic resources are abundant, as it allows waste to be used productively, generating energy and reducing waste.
One of the great advantages of biomass cogeneration plants is their renewable and sustainable nature. By using organic materials, these plants contribute to reducing dependence on fossil fuels and mitigating climate change. In addition, in many industrial applications, heat generation is as important as electricity, and this type of system offers an effective solution.
Biomass plants also help manage agricultural and forestry waste, contributing to the development of circular economies and the responsible management of natural resources.
4. Biogas cogeneration plants
Biogas cogeneration plants harness methane gas produced by the anaerobic decomposition of organic matter, such as agricultural residues, manure or food waste.
The biogas generated is burned in a combustion engine or turbine to produce electricity. The waste heat from this process is used for heating or industrial processes, which increases the overall efficiency of the system.
This type of cogeneration is particularly attractive in rural areas or in facilities where large amounts of organic waste are generated, such as farms or wastewater treatment plants.
Biogas is a renewable energy source that, when harnessed, reduces the release of methane into the atmosphere, a highly potent greenhouse gas. In addition, biogas plants can be an effective solution for the management of organic waste and the production of clean energy, thus contributing to a more circular economy.
Its implementation is ideal in sectors where the production of heat and electricity is simultaneously necessary, such as in industrial food processes or in district heating systems.
5. Internal combustion engine cogeneration plants
Cogeneration plants that use internal combustion engines, usually gas-powered, generate electricity efficiently. These engines are well suited for small and medium-scale applications, such as in industrial facilities, hospitals or commercial buildings.
The operation is similar to that of a conventional engine, where gas is burned to move the engine's pistons, generating electricity. At the same time, the heat produced by the engine is collected and used in industrial processes or for heating.
One of the main advantages of this type of cogeneration is its ability to adapt to different scales and types of energy consumption. They are easy to install and maintain, making them a viable option for smaller installations that require both electricity and heat.
Furthermore, the use of internal combustion engines allows for flexible operation with regard to the available fuels, from natural gas to biogas or even liquid fuels in some cases.
6. ORC (Organic Rankine Cycle) cogeneration plants
ORC-based cogeneration plants use an organic fluid (instead of water) to generate steam and electricity. These facilities are ideal for taking advantage of low-temperature heat sources, such as waste heat from industrial processes or geothermal sources.
The organic fluid in the ORC cycle is vaporized by being heated by waste heat, which drives an electricity-generating turbine. This system is especially useful when exhaust gas temperatures are not high enough to operate a conventional steam turbine.
One of the main advantages of the ORC cycle is that it can be efficiently used with low-temperature heat sources, opening up new opportunities for cogeneration in industrial processes with waste heat at moderate temperatures. In addition, ORC plants are compact and require less space compared to traditional plants, making them an attractive option for smaller facilities or those with space constraints.
This type of cogeneration is increasingly popular in industries such as geothermal, industrial heat recovery and energy efficiency projects.
7. Stirling Engine cogeneration plants
Power plants using Stirling engines are based on a closed-cycle thermodynamic principle that converts heat into mechanical work.
This type of engine is particularly efficient in low-temperature applications, as it operates by expanding and contracting a sealed gas within the engine's cylinders. The heat, usually produced by burning biomass, gas or solar energy, is used to heat the Stirling engine fluid, allowing electricity to be generated while also harnessing the waste heat for other uses.
The main advantage of Stirling power plants is their high efficiency in low temperature heat applications. Their simple design and the fact that they do not require complex cooling systems makes them an attractive option for small cogeneration systems.
Additionally, since they have no moving parts that come into direct contact, they require relatively low maintenance. These plants can be an excellent option for rural or small-scale installations, such as homes or communities looking for sustainable energy solutions.
8. Microturbine cogeneration plants
Microturbines are a power generation technology that uses a small gas turbine to generate electricity and heat. These turbines are especially effective in small and medium-scale applications such as commercial buildings, hospitals or factories.
The microturbine uses natural gas or biogas to generate electricity, and the waste heat can be used for heating or in industrial processes. These plants have the advantage of being compact, modular and easy to install, making them ideal for installations where space is limited or where flexible energy solutions are required.
The main advantage of microturbines is that they can operate efficiently on alternative fuels, making them an attractive option for communities or facilities looking to become more energy self-sufficient. Additionally, their high reliability and low maintenance make them attractive for long-term applications.
They are ideal for small industrial or commercial installations that require both electricity and heating in a continuous and economical manner.
9. Photovoltaic cogeneration plants (with thermal storage)
Photovoltaic cogeneration plants combine solar energy with thermal storage to generate both electricity and heat.
In this type of installation, solar photovoltaic panels capture solar energy to generate electricity, while the heat collected during the day is stored in thermal storage systems, such as molten salts. This stored heat can be used to generate steam or for heating at night or when solar demand is low. This combination allows for a constant supply of both electrical and thermal energy, even when the sun is not available.
This system offers several advantages, including its renewable and sustainable nature, and is particularly useful in areas with high levels of solar radiation. The integration of thermal storage allows these plants to generate heat efficiently throughout the year, even when weather conditions are not ideal.
Combined heat and power plants are gaining popularity as a comprehensive solution for communities, factories and large commercial facilities that require both electricity and heat on a constant basis.
Small and micro cogeneration
-
Small cogeneration: Capacity less than 1 MW.
-
Microcogeneration: Power less than 50 kW, used in homes and small businesses.
The main difference between the two is that in small cogeneration, thermal energy is a by-product of electricity generation, while in micro cogeneration heat is usually the primary need, with electricity as an additional benefit.