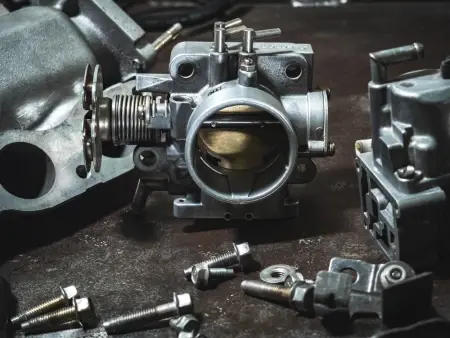
Throttle valves play a key role in thermal engines, especially in controlling the flow of air into the engine. Their function is to regulate the amount of air entering the intake system, which directly affects the air-fuel mixture and, therefore, the performance and efficiency of the engine.
These valves are a key part of the injection and acceleration systems, contributing to the precise adjustment of combustion.
What is a butterfly valve?
A butterfly valve is a device that regulates or interrupts the flow of a fluid (in this case, air) in a conduit. It consists of a circular plate called a "butterfly", which rotates on an axis, thus changing the area through which the fluid passes.
In thermal engines, the throttle valve controls the air flow into the engine, thus adjusting the amount of air that is mixed with the fuel for combustion. When the valve is fully open, the air flow is maximum, and when it is closed, the flow is minimal or even zero.
Operation of butterfly valves in engines
In thermal engines, the throttle valve is usually located in the intake tract, where it regulates the amount of air entering the engine. This component is crucial for controlling acceleration and the air-fuel mixture . When the driver presses the accelerator pedal, the system adjusts the angle of the throttle valve to allow more or less air, depending on the engine's demand.
In older engines, this control is done manually via a cable, while in more modern engines, electronic systems, known as "Drive-by-Wire" , are used to control the valve angle precisely via an electric actuator.
Types of butterfly valves for engines
There are several configurations of butterfly valves used in thermal engines, each suitable for different applications and performance requirements:
- Conventional butterfly valve: The simplest and most common form, where the butterfly rotates around an axis to regulate the air flow. It is widely used in passenger vehicle engines.
- Eccentric Butterfly Valve: In this design, the butterfly shaft is offset, allowing for more effective sealing and greater durability by reducing wear caused by continuous contact between the butterfly and the seat.
- Double Eccentric Butterfly Valve: Used in more advanced applications, this type of valve further reduces friction and improves efficiency by allowing for a more effective seal at the closing point.
- Electronic throttle valve (Drive-by-Wire): This valve uses an electronic control system that allows for more precise regulation of air flow, optimizing engine performance and emissions.
Advantages of butterfly valves in engines
Butterfly valves have several advantages in thermal engines:
- Precise air flow control: This allows for better regulation of the air/fuel mixture, optimising engine efficiency and reducing polluting emissions.
- Quick Response: The throttle valve allows for immediate response to the accelerator pedal, improving driving experience and acceleration.
- Durability: Advanced designs, such as eccentric butterfly valves, improve component durability by reducing wear and friction.
- Electronic Systems Compatibility: Electronic throttle valves allow for easy integration of systems such as traction control, electronic engine management and fuel-saving technologies.
Disadvantages of butterfly valves in engines
Despite their advantages, butterfly valves in engines also have some disadvantages:
- Complexity in electronic systems: Electronic butterfly valves, although more accurate, can increase system complexity and repair cost in the event of electronic failure.
- Maintenance: Although relatively easy to maintain, butterfly valves can accumulate deposits of dirt and debris from the air, which can affect their operation and engine efficiency if not cleaned regularly.
- Leaks: If not sealed properly, throttle valves can experience small air leaks, which can affect the air-fuel mixture and decrease engine performance.
Materials used in butterfly valves for thermal engines
The material used in butterfly valves must be resistant to heat, abrasion and corrosion. It must also offer good thermal conductivity to prevent overheating of moving parts. Some of the most common materials include:
1. Stainless steel
Stainless steel is one of the most commonly used materials for throttle valves in engines, due to its excellent resistance to corrosion, abrasion and high temperatures. This material is ideal for applications where the valves are exposed to severe conditions, such as in the intake systems of thermal engines. In addition, stainless steel has good wear resistance, which extends the life of the valves.
Austenitic stainless steels (such as 304 or 316) are the most common in these cases, due to their ability to resist corrosion in humid environments and their high resistance to heat. However, they are more expensive compared to other materials.
2. Aluminum
Aluminum is another material commonly used in butterfly valve design, especially in engine applications that require lower weight. Aluminum is lightweight and has good thermal conductivity, which helps dissipate heat generated during engine operation. However, its corrosion resistance is lower than that of stainless steel, so it is usually combined with special coatings to improve its durability.
Anodized aluminum is an example of an improvement applied to aluminum, as it provides a protective layer against corrosion and improves wear resistance without significantly affecting its lightness.
3. Composite materials and special coatings
In some more advanced applications, composite materials or special coatings are used on butterfly valves to increase their strength and durability. Tungsten carbide or ceramic coatings may be applied to mating surfaces, such as the butterfly and valve seat, to reduce frictional wear and improve heat resistance.
Additionally, high performance butterfly valves may incorporate copper or graphite inserts to improve thermal conductivity and sealing properties under high pressure and temperature conditions.
4. Special alloys
In high-performance engine applications or racing engines, special alloys are used that combine materials such as nickel and cobalt, which offer excellent resistance to high temperatures and corrosion. These alloys are especially useful in engines that operate at extremely high temperatures or under severe conditions, such as aircraft or racing vehicle engines.
Butterfly valve design in thermal engines
The design of the throttle valve in a thermal engine has to be precise and efficient to ensure proper control of the air flow, optimizing engine performance. Some of the most relevant design aspects include:
1. Type of butterfly
The butterfly valve is the key part of the valve that regulates the flow of air. It can have different shapes and sizes depending on the engine application. The most common shapes include:
-
Circular butterfly: This is the most common design, where the butterfly has a circular shape and rotates on an axis to open or close the air passage. This design is simple, efficient and economical.
-
Disc-shaped butterfly: In some advanced applications, butterflies with a more complex design are used, such as double-eccentric or triple-eccentric discs, which offer greater sealing capacity and lower friction, improving the durability and efficiency of the system.
2. Shaft and control mechanism
The butterfly valve shaft is a critical part of the design as it must be able to withstand the forces generated by the airflow and the movement of the butterfly valve without deforming. The shaft is usually made of high-grade steel or special alloys to ensure strength and durability.
Valve control can be manual, via a throttle cable, or electronic, in modern "Drive-by-Wire" systems. In electronic systems, an electric motor or pneumatic actuator adjusts the throttle angle based on signals sent by the engine ECU. These electronic systems allow for more precise and faster control of airflow, which improves engine response and fuel efficiency.
3. Sealing system
Throttle valve sealing is critical to prevent air leaks that can affect the fuel-air mixture in the engine. Seals are usually made of special rubbers, elastomers or composite materials, depending on the type of valve. In some eccentric throttle valve designs, the angle of the throttle and seat are designed in such a way as to minimize seal wear and improve tightness.
4. Coatings and surface treatments
Butterfly valve design may also include surface treatments to improve performance under extreme conditions. Chromium oxide or titanium nitride coatings may be applied to increase wear, corrosion and friction resistance on the butterfly and seat surfaces.
5. Dimensions and aerodynamic profile
The throttle valve design must also consider dimensions and aerodynamic profile to reduce flow resistance and improve engine efficiency. Throttle valves with more aerodynamic profiles allow for smoother airflow, which reduces energy losses and improves acceleration and overall engine performance.
History and evolution
The butterfly valve was developed during the 19th century as a mechanism for regulating fluid flow in hydraulic and engine systems, although it cannot be attributed to a single inventor.
Its basic design, which allows the flow of a fluid to be controlled by means of a rotating disk, was refined over time and used in a variety of applications, including the steam engines of the Industrial Revolution. In internal combustion engines, its main function is to regulate the air intake into the cylinders to optimize engine performance and efficiency.
Throughout the 20th century, the butterfly valve was improved, especially in the context of thermal engines, with the development of variants such as eccentric valves. Although engineers such as James Watt and other innovators contributed to the evolution of these mechanisms, the design of the butterfly valve was the result of the collaboration of multiple experts over the years.
Today, it remains an essential component in heat engines and other industrial applications.