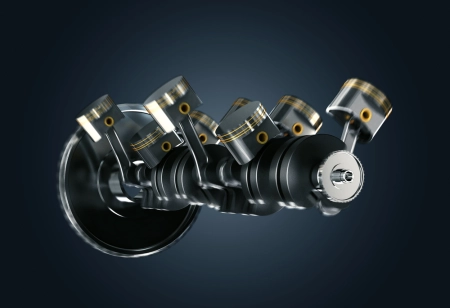
The crankshaft is a fundamental component in thermal engines and reciprocating engines, as it plays a crucial role in converting motion.
This power transmission shaft works like a crank that converts the reciprocating movements of the pistons into rotary movements (as in internal combustion engines) or, in some cases, converts rotary movements into reciprocating movements (as in eccentric mechanical presses).
Function of the crankshaft in a thermal engine
In thermal engines, the crankshaft absorbs the forces generated by the explosions inside the cylinders and, by means of the connecting rods, transforms the alternating linear motion of the piston into a rotary motion. This motion is then transmitted to other engine components, such as the flywheel or the distribution system. The crankshaft must be extremely strong due to the torsional and bending stresses to which it is subjected during operation.
Crankshaft structure and components
A crankshaft is made up of several key elements:
- Journals : The points of attachment between the connecting rods and the crankshaft. Each journal rotates off-center relative to the crankshaft's axis of rotation.
- Counterweights : Placed on the extension of each elbow (or arm), they serve to balance the crankshaft and reduce vibrations.
- Timing pinion and flywheel : These components are mounted on the ends of the crankshaft, allowing coupling with other engine systems.
In a typical four-cylinder engine, the crankshaft usually has five bearings that are attached to the crankshaft bed of the engine block. These bearings, or bedplates, are crucial to keeping the crankshaft in its rotational position and ensuring that it operates without unwanted movement.
Operation of the crankshaft
The crankshaft converts the reciprocating motion of the pistons into a rotational motion thanks to its elbows. These elbows receive the connecting rods, which in turn are connected to the pistons. The journal of each elbow is the axis of rotation of the crankshaft, and through the connection between the journal and the crank arm, rotation occurs.
To compensate for the imbalance caused by the off-center rotation of the crank pins and connecting rods, counterweights are installed at the ends of the crank arms. These counterweights help to balance the forces and reduce unwanted vibrations. On some crankshafts, the elbows are arranged so that the imbalances in one elbow are compensated by those in the other, which facilitates smoother operation.
Materials and manufacturing technology
The crankshaft must be manufactured from high-strength materials, as it must withstand fatigue, torsion and wear. The most common materials are high-alloy steels, such as carbon steel, chromium-manganese and chromium-nickel-molybdenum, due to their high strength and the ability to obtain surface hardness through treatments such as nitriding.
Steel crankshafts : These crankshafts offer high strength, making them ideal for high-performance engines and applications where fatigue is a major concern. Heat treatments such as nitriding increase the hardness of the crankshaft journals, which improves bearing durability.
Cast Iron Crankshafts : These crankshafts are manufactured by casting ductile iron modified with magnesium. They offer advantages such as high damping capacity for torsional vibrations, which may eliminate the need for additional dampers in some engines.
Types of crankshafts
There are two main types of crankshafts, depending on their design and use:
- Composite or separable crankshafts : In these crankshafts, components such as the connecting rod pin can slide, which improves reliability and reduces friction. This type of crankshaft is more common in twin-cylinder engines due to the complexities in its construction.
- Monolithic crankshafts : These are the most commonly used crankshafts in larger engines. They are made from a single piece, which makes manufacturing easier and reduces the overall weight of the crankshaft. They are simpler to manufacture than composite crankshafts.
Heat treatments and hardening
Due to the stresses to which the crankshaft is subjected, it is common for it to undergo heat treatments to improve its durability and strength. These treatments may include nitriding, flame hardening or induction hardening, which increase surface hardness and wear resistance.
Crankshaft maintenance
The crankshaft is an essential component for the operation of any engine, and proper maintenance is crucial to ensuring engine longevity and performance. Maintenance may include regular inspections for wear or damage to journals, counterweights, and bearings.
It is also essential to check that the crankshaft bearings are in good condition, as a worn bearing can cause inefficient operation or even mechanical failure.
A crankshaft with irregular wear or damage to the journals can cause vibrations in the engine, which not only affects performance but can also damage other components. For this reason, dynamic crankshaft balancing is necessary for some high-performance engines, especially for racing or aviation engines.
Relationship with other engine components
The crankshaft is closely related to several other key engine components, such as:
- The timing system : The crankshaft is connected to the timing sprocket, which controls the opening and closing time of the valves. Precise timing between the crankshaft and camshaft is crucial for efficient engine performance.
- The lubrication system : The crankshaft must be properly lubricated to reduce friction wear. The lubrication system, which includes the oil pump, ensures that the crankshaft and other critical components receive adequate oil to operate without excessive friction.
- The connecting rod : The connecting rod transfers the force generated by the explosion of the fuel from the piston to the crankshaft. This component must be perfectly aligned and be able to withstand compression and torsion forces.
Engine efficiency and performance
The crankshaft directly influences engine efficiency, as a well-balanced, high-quality crankshaft reduces vibration and improves smooth operation. Lightweight, balanced crankshafts allow the engine to run more efficiently, which can improve overall performance and reduce fuel consumption.
In addition, the crankshaft has a major impact on engine exhaust emissions. A poorly balanced crankshaft can cause less efficient operation, leading to increased emissions due to incomplete or irregular combustion. An optimized crankshaft contributes to a cleaner, more efficient engine.
Technological advances in crankshafts
Today, technological advances have allowed crankshafts to be lighter and stronger, using materials such as titanium in high-performance engines or electric motors in sports vehicles.
In addition, manufacturing technology has evolved, with 3D printing being used to create complex models of crankshafts and other components, allowing for reduced production costs and improved accuracy.