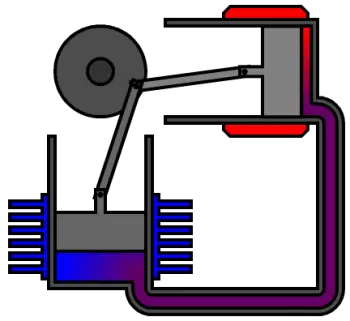
The development of the Stirling engine began as an alternative to the steam engine, motivated by its greater safety and efficiency under certain conditions. Unlike steam engines, which operate at high pressures of superheated water and pose risks of explosion, the Stirling engine uses an external combustion cycle, making it safer and more versatile in its application.
Over time, however, the advantages it offered over the steam engine were not enough to compete with the rise of internal combustion engines, such as Otto and diesel engines, which demonstrated faster response and a more compact design. These limitations have relegated the Stirling engine to specific applications, such as power generation in environments requiring silence, low vibration, or the use of unconventional heat sources.
The Stirling engine has several features that can be considered both advantages and disadvantages depending on its application. Its main strengths and limitations are analyzed below:
Advantages of the Stirling engine
- High thermal efficiency : Theoretically, the Stirling engine can achieve Carnot efficiency, making it more efficient than other heat engines under certain conditions. Its ability to recover waste heat also contributes to its efficiency.
- Quiet, vibration-free operation : By not using internal combustion engines or intake and exhaust valves, the Stirling engine operates more quietly and with less vibration than internal combustion engines. This feature makes it ideal for applications in submarines, home power systems, and noise-sensitive medical devices.
- Versatility in fuel use : It can operate on any heat source, including fossil fuels, biogas, wood, solar, or nuclear energy. This makes it a viable option in environments where access to specific fuels is limited.
- Reduced wear and maintenance : Because it's an external combustion engine, its internal components are less exposed to combustion residue and high temperatures. This reduces the need for frequent maintenance and prolongs the engine's lifespan.
- Operation in low ambient temperatures : It is more efficient in cold environments compared to internal combustion engines, which can experience starting problems in low temperatures. This makes it suitable for use in polar regions and space applications.
- Lower environmental impact : By allowing the use of renewable energy sources and generating fewer polluting emissions, the Stirling engine is a more sustainable alternative compared to other energy conversion technologies.
Disadvantages of the Stirling engine
- Larger volume and weight : Due to the need for heat exchangers and thermal insulation, the Stirling engine tends to be larger and heavier compared to internal combustion engines of equivalent power. This limits its use in transportation vehicles where weight is a critical factor.
- High manufacturing cost : The materials required to build efficient, corrosion-resistant heat exchangers increase production costs. This characteristic makes them less competitive in many commercial applications, especially compared to mass-produced internal combustion engines.
- Slow start-up and limited response : Its operation depends on heat transfer through heat exchangers, which results in longer warm-up times and reduced responsiveness to speed or load changes. This makes it unsuitable for applications requiring rapid start-ups, such as automotive.
- Potential risk of leaks and explosions : Some designs using hydrogen or helium as the working fluid pose a risk of leakage, requiring efficient sealing systems. Additionally, certain configurations can generate flammable mixtures if not designed properly.
- Difficulty in power regulation : The power generated by a Stirling engine depends on the temperature difference between the hot and cold sources. Adjusting this difference quickly and efficiently can be challenging, limiting its applicability in systems that require constant power changes.