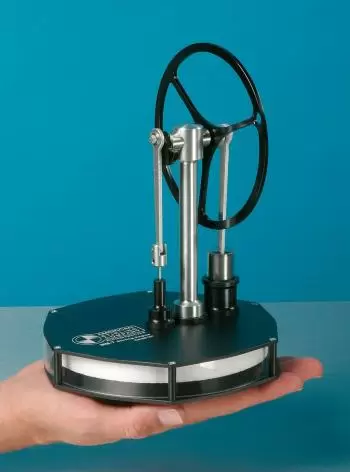
Stirling engine applications can be divided into three main categories:
- mechanical drive
- heating and cooling
- Electric generation systems
A Stirling engine is a heat engine that works by cyclic compression and expansion of air or another gas, the working fluid. During the Stirling cycle there is a net conversion of heat to mechanical work. The Stirling cycle heat engine will also operate in reverse, using a mechanical energy input to drive heat transfer in a reverse direction (ie a heat pump or refrigerator).
Electricity generation using a Stirling engine
Nuclear energy
There is potential for nuclear-powered Stirling engines in electric power generation plants. Replacing nuclear power plant steam turbines with Stirling engines could simplify the plant, produce higher efficiency and reduce radioactive byproducts.
Several breeder reactor designs use liquid sodium as the coolant. If the heat is to be used in a steam plant, a water/sodium heat exchanger is required, which is of some concern as sodium reacts violently with water. A Stirling engine eliminates the need for water at any part of the cycle. This would have advantages for nuclear installations in dry regions.
Solar energy
The Stirling engine sits at the focus of a parabolic mirror, a Stirling engine can convert solar energy into electricity with better efficiency than non-concentrated photovoltaic cells, and comparable to concentrated photovoltaics.
Combined heat and power
In a combined heat and power (CHP) system, mechanical or electrical energy is generated in the normal way, however, the waste heat emitted by the engine is used to supply a secondary heating application. This can be virtually anything that uses low temperature heat. It is often a pre-existing energy use, such as commercial space heating, residential water heating, or an industrial process.
Thermal power plants on the power grid use fuel to produce electricity. However, there are large amounts of waste heat that often go unused. In other situations, high quality fuel is burned at a high temperature for a low temperature application. According to the second law of thermodynamics, a heat engine can generate power from this temperature difference.
In a CHP system, high temperature primary heat enters the Stirling engine heater, then some of the energy is converted to mechanical energy in the engine and the rest goes to the cooler, where it exits at low temperature. The "waste" heat actually comes from the main engine cooler, and possibly from other sources like burner exhaust, if there is one.
The power produced by the engine can be used to run an industrial or agricultural process, which in turn generates waste biomass waste that can be used as free fuel for the engine, reducing waste disposal costs. The overall process can be efficient and profitable.
Strirling motor for mechanical output and propulsion
We analyze different cases in which the Stirling engine is used to obtain mechanical work:
automotive engines
It is often claimed that the Stirling engine has too low a power-to-weight ratio, too high a cost, and too long a starting time for automotive applications. They also have complex and expensive heat exchangers. A Stirling cooler must reject twice as much heat as an Otto engine or diesel engine radiator.
The heater must be made of stainless steel, exotic alloy, or ceramic to withstand the high heating temperatures needed for high power density, and to contain hydrogen gas often used in Stirling cars to maximize power. The main difficulties involved in using the Stirling engine in an automotive application are starting time, throttle response, shutdown time, and weight, not all of which have ready-made solutions.
aircraft engines
Stirling engines may hold theoretical promise as aircraft engines, if high power density and low cost can be achieved. They are quieter, less polluting, gain efficiency with altitude due to lower ambient temperatures, are more reliable due to fewer parts and the absence of an ignition system, produce much less vibration (airframes can last longer) and use safer, less explosive fuels.
However, the Stirling engine often has low power density compared to the commonly used Otto engine and Brayton cycle gas turbine. This problem has been a bone of contention in automobiles, and this performance characteristic is even more critical in aircraft engines.
Electric vehicles
Stirling engines as part of a hybrid electric drive system can avoid the design challenges or drawbacks of a non-hybrid Stirling car.
In November 2007, the Precer project in Sweden announced a prototype hybrid car using solid biofuel and a Stirling engine.
marine engines
The Stirling engine might be suitable for submerged power systems where electrical or mechanical work is required on an intermittent or continuous level. General Motors has done a considerable amount of work on advanced Stirling cycle engines that include thermal storage for subsea applications. United Stirling, in Malmo, Sweden, is developing an experimental four-cylinder engine that uses hydrogen peroxide as an oxidizer in underwater fueling systems.
pump motors
Stirling engines can drive pumps to move fluids such as water, air, and gases. For example, Stirling Technology Inc.'s ST-5 power output of 5 horsepower (3.7 kW) which can run a 3 kW generator or a centrifugal water pump.
Using the Stirling engine for heating and cooling
If supplied with mechanical power, a Stirling engine can work in reverse as a heat pump for heating or cooling. In the late 1930s, the Philips Corporation of the Netherlands successfully used the Stirling cycle in cryogenic applications. Experiments have been carried out using wind power driving a Stirling cycle heat pump for domestic heating and air conditioning.