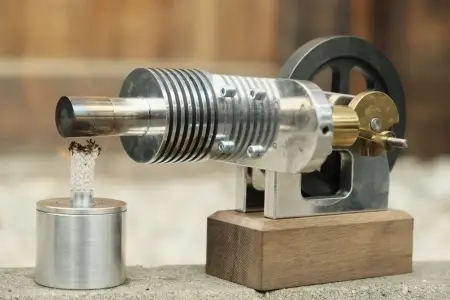
The Stirling engine is a type of heat engine that operates by cyclic compression and expansion of a working gas, usually helium, hydrogen, or air, at different temperatures.
This engine is known for its high efficiency, quiet operation, and ability to operate on a variety of heat sources, including solar energy, fossil fuels, and biomass.
Operating principles: cycle phases
The Stirling engine follows a closed thermodynamic cycle, meaning the working gas does not leave the system. Its operation is based on the conversion of thermal energy into mechanical energy through the expansion and compression of the gas in different temperature chambers.
Unlike internal combustion engines, it does not require explosions or combustion inside the cylinder, making it quieter and more durable.
The Stirling cycle consists of four main phases:
- Isothermal compression : In this phase, the working gas in the cold chamber is compressed at a constant temperature. During compression, the gas releases heat through the cold heat exchanger, which reduces its volume and increases the pressure within the system. This process generally occurs in the coldest part of the engine and is crucial for the cycle's efficiency.
- Isochoric (constant-volume) heating : Once compressed, the gas is transferred to the hot zone of the engine, passing through the regenerator. This component stores some of the residual heat from the previous cycle and transfers it back to the gas, helping to improve the engine's thermal efficiency. During this process, the gas's pressure increases significantly without changing its volume.
- Isothermal expansion : When the gas reaches the heated chamber, it expands at a constant temperature, performing work on a piston or displacer. This phase converts thermal energy into usable mechanical energy, as the gas exerts pressure on the engine's moving components. Isothermal expansion is key to maximizing system power without excessively increasing heat consumption.
- Isochoric cooling : Finally, the gas returns to the cooling chamber, where it loses heat and its pressure decreases. The regenerator helps recover some of the heat before the gas is compressed again in the next phase of the cycle. This process completes the Stirling cycle, ensuring that the engine operates continuously without loss of working gas.
Components of a Stirling engine
Stirling engines can be designed in a variety of ways, but generally consist of the following key elements:
- Heat source : This is the element that supplies the thermal energy needed to initiate and maintain the cycle. This can be an open flame, a solar concentrator, an electric heater, or any other external heat source.
- Heat exchangers : These are used to heat and cool the working gas at different points in the cycle. Heat exchangers include both the hot and cold sides of the engine and play a key role in the efficient transfer of thermal energy.
- Regenerator : This is an internal heat exchanger that improves engine efficiency by storing and releasing heat at strategic points during the cycle. By acting as an intermediate thermal storage, it reduces the amount of heat lost during each cycle and increases overall engine performance.
- Pistons or displacers : These are the mechanical elements that allow the expansion and compression of the gas within the system. Power pistons transform the gas's energy into mechanical motion, while displacers control the flow of gas between the hot and cold zones.
- Expansion and compression chambers : These are the areas where the gas changes temperature and volume. The hot chamber is where the gas expands and generates work, while the cold chamber allows for the gas to be compressed to restart the cycle.
- Driveshaft : Connects the motion of the pistons to a power output mechanism, allowing the Stirling engine to drive electrical generators, cooling systems, or even mechanical devices.
- Seals and bearings : These components ensure that the working gas remains within the system without leaks, which is crucial for engine efficiency and durability. They also minimize friction and mechanical wear.
Stirling engine performance
The performance of a Stirling engine is determined by its thermal efficiency and the conversion of heat into mechanical work. Its maximum theoretical efficiency is limited by the Carnot cycle, which means it can be higher than that of internal combustion engines.
Factors that influence its performance:
- Temperature difference : The greater the difference between the heat source and the cold zone, the greater the efficiency of the engine.
- Materials used : Components with high thermal conductivity improve heat transfer, reducing energy losses.
- Regenerator efficiency : A well-designed regenerator can significantly increase efficiency by minimizing heat losses.
- Friction and leaks : Reducing internal friction and keeping the system tight helps maximize the use of generated energy.
- Operating speed : Although Stirling engines can operate at low speeds with high efficiency, an optimized design can improve their performance at different operating regimes.