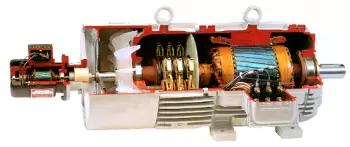
An asynchronous motor is an electric motor powered by alternating current in which the speed of rotation of the rotor is different from that of the magnetic field of the stator. This type of motor is also known as an induction motor.
The induction motor is composed of a rotor and a stator, in which the inductor coils are located. The inductor coils are three-phase and are 120º out of phase with each other.
The asynchronous motor is based on the currents induced in the rotor from the stator's magnetic field; that's why it's called an induction machine.
In order to induce an electric current in the rotor, it is necessary for the rotor to be subjected to a variation in the magnetic flux generated by the stator at the supply frequency, or synchronism. Consequently, the rotor demagnetizes when it reaches synchronism since it does not see magnetic flux variation.
For this reason, the rotor rotates at a different speed than the stator field and therefore rotates asynchronously. In these motors, the rotating magnetic field has a synchronous speed according to the frequency of the feeder line.
An important characteristic of the asynchronous or induction motor is that the speed of the rotor, and therefore the power, cannot be varied gradually. The operating speed of induction motors depends on the supply frequency and the number of poles.
Why are asynchronous motors the most used in the industry?
Induction motors are the most widely used motors in the industry due to their robustness and price, especially the three-phase asynchronous motor. This success is mainly due to the following reasons:
- Compared with other electric motors of the same power, its cost is lower.
- These are engines of great simplicity with great ease of maintenance.
- The asynchronous motor has better performance compared to the single-phase motor. For this reason, the single-phase motor is relegated to small power appliances and household appliances.
Induction motors are also widely used in the construction of electric vehicles.
How does an induction motor work?
The stator coil is powered by an alternating current. Thanks to the arrangement of the pole pairs, out of phase with each other, the current generates a general magnetic field that rotates in space with the same frequency as the supply current. This magnetic field is called the stator field or rotating field.
The rotor winding is immersed in this rotating magnetic field. Since the rotor rotates slower than the stator field, the magnetic flux subtended by the rotor winding varies; consequently, the rotating magnetic field induces currents in the rotor by magnetic induction (Faraday's law).
These induced currents, in turn, generate a rotor magnetic field, which opposes flux variations. The rotor's magnetic field interacts with the stator field, generating a torque in the rotor winding that causes the rotor to turn. The rotation of the rotor provides the mechanical energy that we can take advantage of.
In fact, according to Lenz's law, the induced magnetic field in the rotor always has the opposite direction with respect to the stator.
Induction in the rotor can only occur if the relative velocities of the stator and rotor fields are different. For this reason, the rotor always rotates at a speed lower than that of the rotating field.
Asynchronous motor types
The classification between different types of asynchronous motors depends on the voltage of the alternating current that is used:
- Three-phase asynchronous motor. This type of motor uses 400 volt three-phase current .
- Single-phase asynchronous motor. This type of motor uses 230 volt single current.
Three-phase motors
A three-phase motor is a robust type of motor that does not require a commutator. Most three-phase asynchronous motors have a balanced load. They are motors that consume the same in all three phases, whether they are connected in a star or in a triangle.
For a three-phase asynchronous motor, it can be started in different ways: star-delta, with a frequency inverter, by stator resistors or by rotor resistors.
The voltages in each phase in this case are equal to the result of dividing the line voltage by the root of three. For example, if the line voltage is 400 volts, then the voltage of each phase is 230 volts.
Squirrel cage motor
The squirrel cage motor is a type of asynchronous motor that uses a rotor called a squirrel cage rotor. This type of rotor is made up of a series of bars arranged in the grooves of the rotor ring, joined at their ends to two rings. The starting torque is small and the current they absorb is high.
The vast majority of asynchronous motors are squirrel cage motors.
Wound rotor motor
The wound rotor motor is a type of alternating current electric motor. In this type of motor the rotor ring grooves are inserted into the windings joined by a common point. This type of motor has copper rings, called slip rings, that rotate with the shaft making contact between it and some brushes that will allow the rotor windings to be connected to the outside.
The advantage of the wound rotor is that they allow progressive starting by means of rotor resistors. However, nowadays, with the use of electronic starters and variators they are not necessary and their manufacture is very limited.