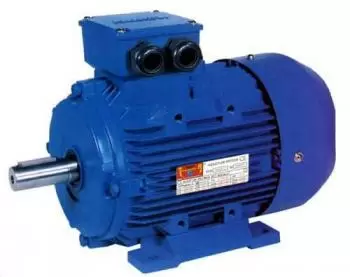
An alternating current (AC) motor is an electric motor that is powered by alternating current. Electric motors convert electricity into rotating mechanical work through the interaction of the magnetic fields of the stator and rotor.
The most widely used motors are alternating current. Those of direct current (or direct current) are used for special machines such as boats or in small machines where a significant range of rotation speed is desired.
Types of alternating current motors
There is a wide variety of alternating current motors, among them the following basic types stand out:
Universal motor
The universal motor is a type of motor that works with single-phase alternating current but can also work with direct current (DC).
Its structure resembles that of a direct current (DC) series motor with some variations:
-
The polar cores and the magnetic circuit in general are made of silicon iron plates. These sheets are stacked and insulated to avoid energy losses due to eddy currents. Eddy currents are generated due to variations in the magnetic flux generated when connecting the motor to the electrical network.
-
The inductor has fewer turns to prevent the core from becoming magnetically saturated. In this way, the energy losses due to eddy currents and hysteresis are reduced. In addition, reducing the turns increases the motor torque due to the increase in the intensity of electric current.
-
The armature has more turns in the armature in order to compensate for the drop in flow as a consequence of the fewer number of turns in the inductor.
The use of this single-phase motor is very common since it has a higher starting torque compared to induction motors. Another advantage is the high speed of rotation that facilitates the reduction of the size of the motor and the price. The most widespread use is in small and portable machines of all kinds.
Synchronous motor
The speed of rotation of the rotor is constant and proportional to the frequency of the voltage of the electric current to which it is connected. This speed is known as "sync speed".
The rotor can be of two types:
-
Permanent magnet synchronous motor.
-
Wound motor in which magnets are replaced by electromagnets.
The motor winding is located on the stator. When electric current flows through the winding, a magnetic field is generated that interacts with the magnets (or electromagnets) of the rotor.
Synchronous motors work much like an alternator.
This type of motor works with three-phase currents that can be connected to the electrical current with star-delta connections.
The name of a synchronous motor is due to the fact that the rotor rotates at the same speed as the magnetic field of the stator. The main application is in large machines with variable load and need to maintain a constant speed.
Asynchronous motor or induction motor
The asynchronous motor has the characteristic that the speed of rotation of the rotor is lower than the speed with which the rotating magnetic field caused by the electric current flowing through the stator coil rotates.
This type of motor is also known as an induction motor because it can function as an alternator. If we apply an external force to the rotor so that it acquires a speed of rotation higher than that of the magnetic field of the stator, the motor works as if it were an asynchronous electric generator.
It is commonly used for applications that:
-
They need small powers
-
Ease of use is prioritized over using a synchronous motor that requires a current inverter. In this case, the asynchronous motor is more inefficient. However, the efficiency of these motors depends on the maximum power and decreases as the number of poles increases. Typically for three phase motors this variation is 0.67 to 0.97 for larger motors.