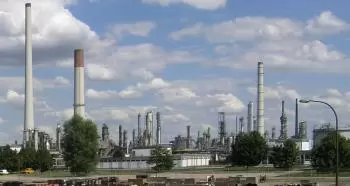
An oil refinery is an industrial plant that transforms crude oil into useful products through processes such as distillation and purification. Through techniques such as normal pressure and vacuum distillation, oil is separated into fractions with a defined boiling range.
These fractions are further refined using methods such as chemical extraction or cleaning. To improve the quality of the products, such as the octane number, conversion processes such as isomerization or catalytic reforming are used. In addition, additives are added to the products to improve or modify certain properties.
Products obtained include high-value fuels such as gasoline, diesel, kerosene and gas oil. Raw materials for the chemical industry such as liquefied petroleum gas, naphtha and middle distillates are also generated.
Oil refineries are large industrial complexes, consisting of tanks, rectification columns, piping systems and flares. These businesses are very energy-intensive, as up to 50% of production costs come from energy, which is supplied mainly from the energy products themselves.
Oil: the raw material of a refinery
The raw material of a refinery is crude oil, a complex mixture of hydrocarbons. The main types of hydrocarbons present are alkanes (paraffins), cycloalkanes (naphthenes) and aromatics. Each type of oil has a specific chemical composition that depends on its origin, which also influences its physical properties, such as colour and viscosity.
Crude oil also contains nitrogen, oxygen and sulfur compounds, such as amines, porphyrins, mercaptans, thioethers, alcohols and quinones. In addition, it may contain traces of metals such as iron, copper, vanadium and nickel. The proportion of pure hydrocarbons varies between 97% and 50% in the heavier oils. The carbon content is between 83% and 87%, and the hydrogen content is between 10% and 14%. Other elements, such as metallic compounds, are generally less than 1000 ppm.
Crude oil varies by region. Well-known examples include West Texas Intermediate (WTI), a light, low-sulfur crude; Brent Blend, from the North Sea; and Malaysia's Tapis and Indonesia's Minas heavy crude, among others.
What products are obtained in a refinery?
The finished products of a refinery can be gaseous, liquid or solid.
In a modern refinery, approximately 3% of the products are liquefied gases such as propane and butane, 9% are by-products such as naphtha, and 24% is gasoline. Other products include kerosene (4%), diesel (21%), heavy fuel oil (11%), and solid products such as bitumen (3.5%) and lubricants (1.5%).
Product yields depend on the nature of the crude oil processed and the refinery configuration. Light crude oils, for example, produce more light products such as LPG, gasoline and kerosene, while heavy crude oils produce more heavy products such as fuel oil. In addition, modern refineries can use processes such as cracking to convert these heavy products into lighter ones.
How does an oil refinery work?
Crude oil extracted from the deposits undergoes preliminary treatment to remove impurities such as sediment and water. It is then transported to the refinery, where it undergoes a distillation process to separate its components into fractions with different boiling points. These components are then processed to produce finished products.
One of the by-products of the process is refinery gas, which is used as an energy source in furnaces or in chemical processes.
Purification and desalination of petroleum
Prior to distillation, crude oil is desalted to prevent corrosion in the equipment. This process involves adding water to the crude oil to form an emulsion that is separated in an electrostatic desalter. The desalted crude oil is then pumped to the distillation unit.
Primary processing: Distillation of crude oil
The desalted crude oil is heated in two stages: first in heat exchangers, then in furnaces to around 400°C. It is then subjected to distillation in a column up to 50 metres high. In this process, the crude oil is separated into different components according to their boiling points, such as petrol, kerosene, diesel and residues.
The residues from this first distillation are subjected to vacuum distillation to obtain products such as vacuum diesel and other by-products.
Conversion and mixing processes
To improve product quality and remove contaminants such as sulfur and nitrogen, additional processes such as hydrotreating, catalytic reforming, isomerization and alkylation are used.
- Hydrotreating: Crude oil is treated with hydrogen to remove sulfur and nitrogen compounds.
- Catalytic reforming: This process improves the octane rating of gasoline and produces aromatic hydrocarbons, in addition to generating hydrogen.
- Isomerization: Alkanes are converted to isoalkanes to improve octane.
- Alkylation: Isoalkanes and alkenes combine to form higher molecular weight, high octane hydrocarbons.
Cracking
Thermal cracking, catalytic cracking, and hydrocracking are used to break heavy hydrocarbon chains and produce lighter products such as gasoline and diesel. In thermal cracking, heat is applied without catalysts, while in catalytic cracking and hydrocracking, catalysts are used to accelerate the reactions.